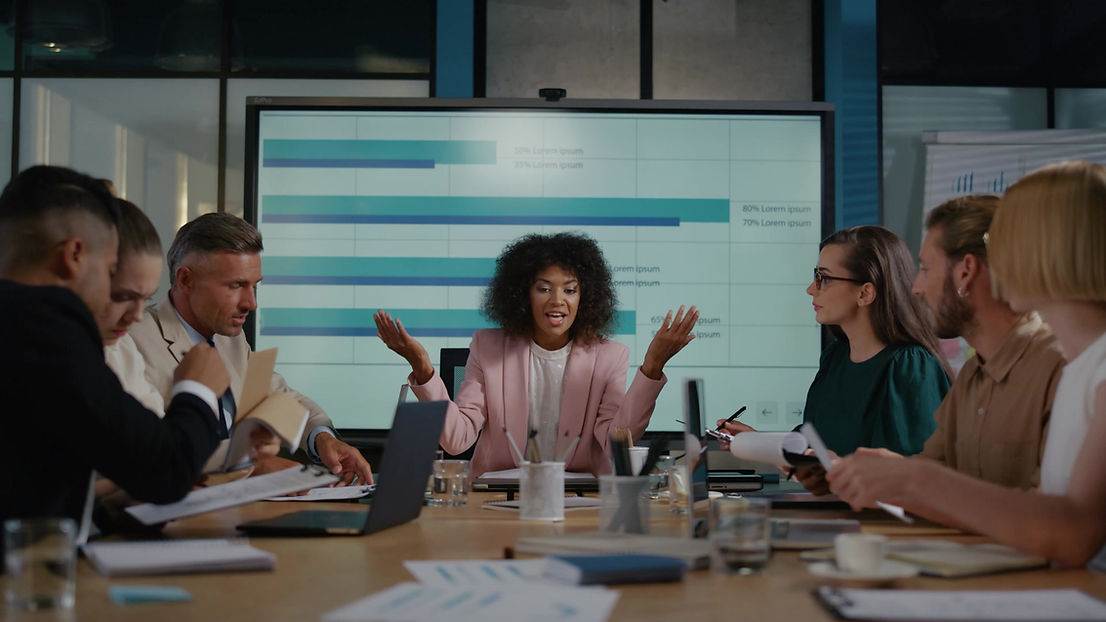
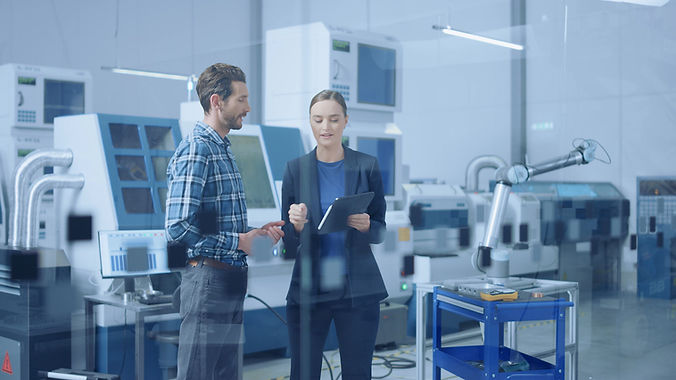
Manufactoring
-
Product development, production planning, and supply chain management.
​
-
Optimize workflows and ensure quality control.
Case Study: Precision Dynamics - Seamless Expansion and Digital Twin Integration in Manufacturing
​
Executive Summary:
Precision Dynamics, a leading manufacturing company, faced the complex challenge of simultaneously constructing new manufacturing centers and implementing cutting-edge digital twin technologies. This required bridging the physical construction with the digital integration, minimizing disruption to ongoing production, and ensuring a smooth transition to the new, digitally enhanced facilities. Leveraging a modern project management platform, Precision Dynamics achieved a seamless rollout, significantly improving overall company performance and reducing downtime.
​
Challenges:
-
Simultaneous Construction and Technology Integration: Managing the construction of new manufacturing centers while integrating digital twin technologies into existing centers.
-
Minimizing Production Disruption: Ensuring minimal impact on daily manufacturing operations during the rollout.
-
Complex Interdependencies: Coordinating construction, equipment installation, digital twin integration, and staff training.
-
Real-time Data Synchronization: Ensuring seamless synchronization between physical construction progress and digital twin development.
-
Predictive Risk Mitigation: Proactively identifying and mitigating potential risks associated with construction delays, equipment malfunctions, and digital integration errors.
-
Resource Optimization: Efficiently allocating resources across construction projects, digital twin development, and ongoing production.
-
Data-Driven Decision Making: Making informed decisions based on real-time data from construction, production, and digital twin simulations.
​
Solutions Implemented:
-
Hierarchical Project Decomposition: The platform was used to break down the project into manageable portfolios, programs, and individual projects, including construction phases, equipment installations, and digital twin module development.
-
Stackable, Reusable Templates: Customizable templates were created for construction phases, equipment installations, digital twin module deployment, and quality control processes, ensuring consistency and efficiency.
-
Portfolio Level:
-
The portfolio level encompassed the entire modernization initiative.
-
-
Program Level:
-
The program level was established to aggregate all activities for each manufacturing center and all associated projects supporting resource constrains at all locations allowing for corporate to identify where to dispatch additional resources to support both technical cloud integrations and human resource partners for training. ​
-
-
Project Level:
-
Project Templates: Project level templates were setup encompassing various floor layouts and configurations for the new center buildout and separate project templates for the digital twin integration for each machine type that every location ensuring each location had the correct information and associated procedures, hand books, training, and required certifications for each team member.​
-
-
-
Predictive Risk Analysis: AI-driven risk analysis identified potential risks associated with construction delays, equipment malfunctions, and digital twin integration errors, enabling proactive mitigation.
-
Value Management: Real-time tracking of construction progress, equipment installation, digital twin simulations, and production output provided insights into resource utilization and project performance.
-
Accelerated Workflows and Interdependency Management: Advanced scheduling tools and dependency mapping features ensured seamless coordination between construction teams, equipment installers, and digital twin developers.
-
Enhanced Collaboration and Communication: The cloud-based platform facilitated real-time communication and collaboration among all stakeholders, including construction managers, engineers, production teams, and digital twin developers.
-
Data-Driven Decision Making: Real-time dashboards provided comprehensive project data, enabling informed decisions regarding resource allocation, construction timelines, and digital twin optimization.
​
Results:
-
Seamless Technology Integration: Digital twin technologies were successfully integrated with new manufacturing centers without disrupting ongoing production for existing centers.
-
Minimized Production Downtime: Proactive risk mitigation and efficient coordination minimized production downtime during the rollout.
-
Improved Project Efficiency: Streamlined workflows and reusable templates reduced project timelines and costs.
-
Enhanced Resource Optimization: Real-time data and value management enabled efficient resource allocation across all project phases.
-
Proactive Risk Mitigation: AI-driven risk analysis minimized construction delays and digital twin integration errors.
-
Improved Communication and Collaboration: Real-time communication and collaboration tools enhanced team coordination and information sharing.
-
Data-Driven Performance Improvement: Informed decisions based on real-time data from digital twin simulations and production metrics improved overall company performance.
Conclusion:
By implementing a modern project management platform, Precision Dynamics successfully navigated the complex challenge of building new manufacturing centers and integrating digital twin technologies. The platform's advanced features enabled Precision Dynamics to minimize disruption to ongoing production, optimize resource allocation, and make data-driven decisions, ultimately improving overall company performance and reducing downtime. This case study demonstrates the transformative power of modern project management technology in the manufacturing industry, driving faster, more reliable, and more profitable operations.
This case study is a fictionalized representation of potential outcomes and is intended for demonstrative purposes only.
The Future of Work:
Unleashing Team Potential

Reduce project costs by accelerating delivery through automated workflows and intelligent task assignments.

Improve efficiency by providing hyper-personalization and embedding relevant knowledge directly into workflows.

Optimize resource allocation and eliminate inefficiencies by gaining real-time visibility across the organization, from small teams to large enterprises.